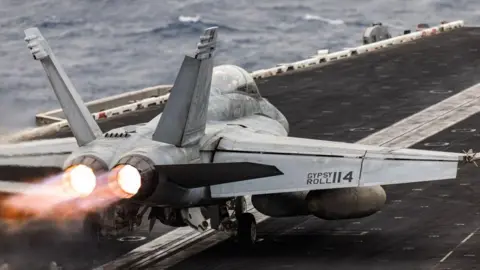
Os motores a jato são um dos feitos de engenharia mais incríveis que os humanos já realizaram.
Mas os motores a jato não deveriam ser possíveis, diz Ben Beake, diretor de pesquisa de materiais da Micro Materials, que testa o equipamento no País de Gales.
“O ar que entra é mais quente do que o ponto de fusão do metal que está por baixo – o que obviamente não é bom”, explica, salientando que este ar atinge temperaturas bem acima dos 1000ºC.
Os projetistas de motores a jato contornaram esse problema aplicando revestimentos cerâmicos resistentes ao calor nas pás do motor. E agora os investigadores estão a desenvolver revestimentos ainda mais fortes que permitem que os motores funcionem ainda mais quentes.
“Se você se aquecer, haverá uma enorme economia de combustível e CO2”, diz o Dr. Bico. Ele estima que aumentando a temperatura em apenas 30°C, você pode economizar 8% em combustível.
Este é o poder dos revestimentos – eles mudam radicalmente a funcionalidade e as capacidades do material subjacente. Poucas pessoas percebem o quão importantes eles são, mas esses revestimentos e folheados podem sobrecarregar máquinas de alto desempenho ou garantir que equipamentos caros sobrevivam aos ambientes mais adversos.
Dr. Beake e seus colegas têm a missão de levar os revestimentos ao limite para ver quão robustos e eficazes eles realmente são. Seus clientes nem sempre alcançam os resultados desejados. Ele se lembra de ter dito a um fabricante de foguetes há vários anos: “Quebramos seu revestimento”. “Eles invadiram”, diz o Dr. Beake.
Além de expor os revestimentos a altas temperaturas, a Micro Materials também possui um dispositivo “pica-pau”, uma pequena ponta de diamante que bate repetidamente no revestimento em locais aleatórios para testar sua durabilidade.
Recentemente, a empresa trabalhou com a Teer Coatings, sediada no Reino Unido, para testar um produto que poderia ser aplicado a componentes de satélites, incluindo engrenagens e rolamentos usados em diversas peças móveis.
É uma tarefa difícil, diz Xiaoling Zhang, da empresa, porque o revestimento deve proteger esses componentes tanto antes do lançamento (quando expostos à umidade atmosférica ao nível do solo) quanto em órbita, contra partículas de poeira e radiação no espaço. No entanto, ele afirma que a empresa tem alcançado os resultados desejados.
Mas, além de proteger as naves espaciais, os revestimentos também podem evitar que os astronautas adoeçam.
Biofilmes – o terrível acúmulo de bactérias dentro dos canos – eles crescem mais rápido em ambientes de baixa gravidadeo que poderia ser um problema, por exemplo, para o abastecimento de água ou máquinas que transportam fluidos em estações espaciais ou futuras naves espaciais.
“Sabe-se que os biofilmes causam falhas mecânicas”, diz Kripa Varanasi, do Instituto de Tecnologia de Massachusetts. “Você não quer isso.
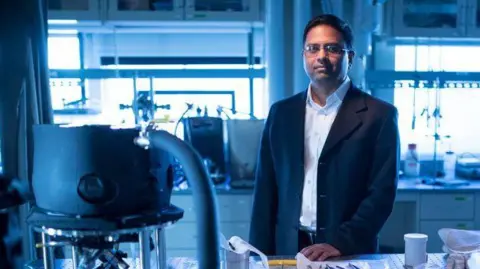
O professor Varanasi e seus colegas desenvolveram uma série de revestimentos que tornam as superfícies escorregadias e, portanto, resistentes à formação de biofilme. Testes de um desses revestimentos em um experimento realizado a bordo da Estação Espacial Internacional descobriram que ele não funcionou como pretendido.
O objetivo do revestimento é misturar o material sólido e o lubrificante. Isso é então pulverizado no interior do cano ou tubo, tornando a superfície interna extremamente escorregadia.
O professor Varanasi já foi manchete por desenvolver revestimentos semelhantes o interior das embalagens de pasta de dente – para que você possa obter até a última gota de pasta de dente. Ele e seus colegas comercializaram a tecnologia por meio de sua empresa spin-out, a LiquiGlide.
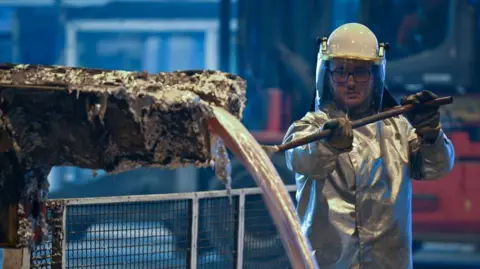
O escorregadio talvez seja um atributo subestimado. Nuria Espallargas, da Universidade Norueguesa de Ciência e Tecnologia, e colegas desenvolveram um revestimento à base de carboneto de silício para equipamentos utilizados na produção ou reparo de alumínio.
É uma solução do tipo panela antiaderente, o que significa que nenhuma camada de alumínio fundido gruda neste dispositivo caro. No entanto, o funcionamento exacto deste revestimento específico é actualmente um mistério.
“Para ser sincero, não sabemos realmente como funciona, o mecanismo é desconhecido neste momento”, diz o professor Espallargas.
No entanto, o revestimento está disponível comercialmente através de sua empresa spin-out, Seram Coatings. A Atlas Machine and Supply, empresa americana que fabrica e repara máquinas industriais, experimentou.
“O verdadeiro benefício está em prolongar a vida útil da ferramenta e melhorar a qualidade dos produtos fabricados”, afirma Jeremy Rydberg, Diretor de Inovação.
Ele diz que sem o revestimento, a Atlas precisa refazer as ferramentas de rolo que usa para usinar alumínio a cada dois dias. Isso custa US$ 4,5 milhões por ano. Mas o novo revestimento significa que as ferramentas duram uma semana, e não apenas alguns dias, reduzindo os custos de reconstrução para cerca de 1,3 milhões de dólares por ano.

Os revestimentos podem fazer coisas incríveis, mas nem sempre funcionam como pretendido, observa Andy Hopkinson, diretor administrativo do Safinah Group, que é frequentemente chamado para investigar quando os revestimentos dão errado.
“Estamos vendo muitos problemas com estacionamentos hoje em dia, onde o sistema passivo de proteção contra incêndio está descascando”, diz ele, referindo-se ao revestimento resistente ao fogo às vezes aplicado em estruturas de concreto.
E a sua empresa também descobriu que os revestimentos aplicados em navios comerciais nem sempre impedem que as baleias e outras formas de vida marinha se fixem no casco. Este problema, conhecido como bioincrustação, aumenta o atrito, o que significa que o navio esfrega o motor tem que trabalhar mais – e queimar mais combustível.
Apesar da disponibilidade de revestimentos que prometem ajudar, nem sempre os proprietários de barcos escolhem o mais adequado para sua embarcação. Essa escolha deve depender de onde o navio está navegando, por quanto tempo deve ficar ocioso em vez de se mover, e assim por diante, diz o Dr. Hopkinson.
O custo de lidar com esses problemas pode chegar a milhares ou até milhões de libras. “Normalmente a pintura custa entre 1 e 2% do projeto. O problema é que quando tudo corre mal, os custos tornam-se exponenciais”, afirma Hopkinson.
No entanto, os investigadores que trabalham nesta área afirmam que ainda existem muitas oportunidades para melhorar os revestimentos e desenvolver novos que possam melhorar significativamente o desempenho das máquinas ou infraestruturas no futuro.